图书介绍
注塑成型实用手册2025|PDF|Epub|mobi|kindle电子书版本百度云盘下载
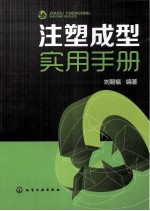
- 刘朝福编著 著
- 出版社: 北京:化学工业出版社
- ISBN:7122172488
- 出版时间:2013
- 标注页数:471页
- 文件大小:261MB
- 文件页数:488页
- 主题词:
PDF下载
下载说明
注塑成型实用手册PDF格式电子书版下载
下载的文件为RAR压缩包。需要使用解压软件进行解压得到PDF格式图书。建议使用BT下载工具Free Download Manager进行下载,简称FDM(免费,没有广告,支持多平台)。本站资源全部打包为BT种子。所以需要使用专业的BT下载软件进行下载。如BitComet qBittorrent uTorrent等BT下载工具。迅雷目前由于本站不是热门资源。不推荐使用!后期资源热门了。安装了迅雷也可以迅雷进行下载!
(文件页数 要大于 标注页数,上中下等多册电子书除外)
注意:本站所有压缩包均有解压码: 点击下载压缩包解压工具
图书目录
第1章 塑料与塑料制品1
1.1塑料的成分及配制1
1.1.1塑料的成分1
1.1.2塑料的配制3
1.2塑料中的高聚物3
1.2.1高聚物的分子结构与聚集态3
1.2.2高聚物在成型过程中的流动特性5
1.2.3高聚物成型过程中的取向6
1.2.4高聚物成型过程中的降解8
1.2.5高聚物成型过程中的交联反应9
1.3塑料的类别及性能10
1.3.1塑料的类别及命名10
1.3.2塑料的使用性能11
1.3.3热塑性塑料的结晶特性13
1.3.4热塑性塑料的成型性能14
1.3.5热固性塑料的成型性能17
1.3.6塑料受热时的三种状态19
1.3.7塑料的改性及性能20
1.4常用塑料及其性能21
1.5塑料的检测与选用27
1.5.1塑料熔体流动性能的检测27
1.5.2常用塑料的简易辨别方法27
1.5.3常用塑料的性能32
1.5.4塑料的选用32
1.6塑料制品33
1.6.1塑料制品的成型工艺性要求33
1.6.2壁厚33
1.6.3过渡圆角35
1.6.4加强筋35
1.6.5 孔35
1.6.6螺纹36
1.6.7嵌件36
1.6.8压花37
1.6.9塑料制品自攻螺钉预留底孔直径38
1.6.10塑料制品尺寸公差值38
第2章 注塑机及其周边设备40
2.1注塑机的基本结构与类型40
2.1.1注塑机的基本结构40
2.1.2注塑机的工作过程41
2.1.3注塑机的类型与规格41
2.2注塑机的注射装置45
2.2.1 注射装置的技术参数45
2.2.2塑化机构的类型48
2.2.3螺杆49
2.2.4螺杆头54
2.2.5料筒55
2.2.6喷嘴57
2.2.7注射装置的典型结构61
2.3注塑机的合模装置64
2.3.1合模装置的功能与类型64
2.3.2合模装置的技术参数66
2.3.3曲肘连杆式合模装置69
2.4新型注塑机74
2.4.1全电驱动注塑机74
2.4.2微型精密注塑机75
2.5注塑机的选择76
2.5.1常见注塑机品牌76
2.5.2注塑机的选型要点78
2.6注塑机周边设备79
2.6.1热风循环烘箱79
2.6.2远红外线干燥箱79
2.6.3热风料斗干燥器80
2.6.4除湿干燥机80
2.6.5自动供料机80
2.6.6模具温度控制机81
2.6.7破碎机81
2.6.8取件机械手82
2.7注塑机的调试82
2.7.1注塑前的准备与检查82
2.7.2模具的安装84
2.7.3注塑机运行过程中的注意事项85
2.7.4注塑机的停机操作85
2.7.5模具的拆卸86
2.8注塑机的操作与使用(以克劳斯玛菲牌注塑机为例)86
2.8.1克劳斯玛菲牌注塑机简介86
2.8.2注塑机的操作系统87
2.8.3注塑机的参数设置89
2.8.4注塑机的维护115
2.9注塑机的保养与维护(以海天牌注塑机为例)133
2.9.1保养与维护计划133
2.9.2日常检查133
2.9.3螺杆和料筒的保养135
2.9.4合模装置的保养140
2.9.5液压系统的保养140
2.9.6润滑系统的保养141
2.9.7电控系统的维护144
2.9.8滑脚(减振垫铁)的调整144
2.9.9管路检测145
2.9.10保养和维护时的注意事项146
第3章 注塑模具的结构与使用147
3.1注塑模具的基本结构与类型147
3.1.1注塑模具的基本结构147
3.1.2注塑模具的类型148
3.2注塑模具的模架151
3.2.1模架的结构151
3.2.2标准模架的类别153
3.2.3富得巴模架与龙记模架对照155
3.3注塑模具的型腔排列155
3.3.1平衡式排列155
3.3.2非平衡式排列158
3.3.3型腔排列的注意事项158
3.4注塑模具的浇注系统161
3.4.1浇注系统的组成161
3.4.2浇注系统的总体要求161
3.4.3主流道162
3.4.4冷料井162
3.4.5分流道163
3.4.6浇口165
3.4.7浇口的位置169
3.4.8浇注系统的流动平衡173
3.4.9一模多腔流动平衡示例175
3.4.10单型腔流动平衡实例175
3.5注塑模具的导向与定位机构177
3.5.1导柱导套导向机构177
3.5.2锥面对合导向机构179
3.5.3斜面对合精确定位机构180
3.5.4 HASCO定位块示例181
3.5.5 HASCO定位锁示例182
3.6控制三板模开模顺序的定距机构183
3.6.1弹簧-拉杆式定距机构183
3.6.2弹簧-滚柱式定距机构184
3.6.3弹簧-摆钩式定距机构184
3.6.4压块-摆钩式定距机构185
3.6.5拨杆-摆钩式定距机构186
3.6.6拨板-摆钩式定距机构186
3.6.7滚轮-摆钩式定距机构187
3.6.8胶套摩擦式定距机构187
3.6.9滑块式定距机构187
3.6.10三板模拉杆长度的计算188
3.6.11 HASCO标准定距机构组件示例189
3.7注塑模具的侧向抽芯机构190
3.7.1侧向抽芯机构的类型190
3.7.2抽芯过程中脱模力的计算191
3.7.3抽芯距离的计算192
3.7.4斜导柱侧向抽芯机构(行位机构)193
3.7.5侧向抽芯过程中的干涉现象及对策200
3.7.6弯销侧向抽芯机构201
3.7.7斜滑槽侧向抽芯机构202
3.7.8瓣合模(哈呋模)的结构203
3.7.9齿轮齿条水平侧向抽芯机构204
3.7.10齿轮齿条倾斜侧向抽芯机构204
3.7.11齿轮齿条圆弧抽芯机构206
3.8行位机构的应用经验206
3.8.1行位机构的名称来源206
3.8.2前模行位机构应用经验206
3.8.3后模行位机构应用经验208
3.8.4内模行位机构应用经验209
3.8.5防止行位机构与其他部件发生干涉的方法209
3.8.6提高行位机构可靠性的方法211
3.9注塑模具的斜顶杆机构212
3.9.1斜顶杆机构的工作原理212
3.9.2斜顶杆机构的类型与结构213
3.9.3斜顶杆机构的主要参数214
3.9.4斜顶杆无法脱模或者无法退出的原因214
3.10注塑模具的脱模机构(推出机构)216
3.10.1脱模机构的总体要求216
3.10.2推杆的结构形式216
3.10.3推杆的布置217
3.10.4推杆的固定与配合218
3.10.5推杆、扁推杆脱模注意事项219
3.10.6推管脱模机构220
3.10.7推管的结构220
3.10.8推管的固定与配合220
3.10.9推块脱模机构221
3.10.10推件板脱模机构222
3.10.11推出机构的导向222
3.10.12多元件联合脱模机构224
3.11注塑模具的二次脱模机构224
3.11.1弹簧式二次脱模机构224
3.11.2八字形摆杆二次脱模机构225
3.11.3斜楔滑块式二次脱模机构225
3.11.4二次脱模注意事项226
3.11.5二次脱模机构示例226
3.11.6双脱模机构228
3.12螺纹塑件的脱模机构229
3.12.1 强制脱模229
3.12.2瓣合式脱模229
3.12.3齿轮齿条脱螺纹机构230
3.13水口料脱出机构232
3.13.1 利用拉料杆拉断水口料机构232
3.13.2利用斜窝拉断水口料机构232
3.13.3利用推板切断水口料机构232
3.13.4潜伏式浇口凝料脱出机构233
3.14复位与先复位机构233
3.14.1复位杆复位机构233
3.14.2弹簧复位机构234
3.14.3弹簧式先复位机构234
3.14.4连杆式先复位机构235
3.14.5楔形杆——三角滑块式先复位机构235
3.15注塑模具的冷却236
3.15.1 模具型腔壁上的温差236
3.15.2塑件质量与注塑时间的关系236
3.15.3塑料的热扩散系数及对应模具温度236
3.15.4塑件壁厚与冷却时间的关系237
3.15.5常用塑料的热扩散系数、传热系数、比热容和密度237
3.15.6冷却水道在稳定紊流下的流速与流量237
3.15.7水孔中心位置与型腔压力238
3.15.8冷却水道的布置形式238
3.15.9常用模具材料的热导率240
3.15.10冷却介质体积流量的计算240
3.15.11冷却回路传热面积的计算241
3.15.12冷却回路总长度的计算241
3.15.13冷却系统的结构要点242
3.15.14型腔的冷却回路244
3.15.15普通型芯的冷却回路245
3.15.16特殊型芯的冷却回路246
3.15.17冷却水道的连接与密封247
3.15.18冷却系统实例248
3.16注塑模具的排气251
3.16.1排气系统的重要性251
3.16.2排气槽排气251
3.16.3利用分型面排气252
3.16.4利用顶针排气252
3.16.5利用镶拼间隙排气252
3.16.6透气钢排气253
3.17热流道注塑模具253
3.17.1 热流道注塑成型的原理及特点253
3.17.2热流道注塑成型对塑料原料的要求254
3.17.3热流道注塑模具的基本结构254
3.17.4绝热流道注塑模结构示例255
3.17.5热流道注塑模的使用要点256
3.17.6热流道注塑模的浇口套260
3.17.7热喷嘴和热流道板示例263
3.18新模具的试模265
3.18.1试模的准备工作265
3.18.2试模流程及参数调试266
3.18.3试模注意事项267
3.18.4模具的验收267
3.19模具的安装、使用与维护267
3.19.1模具的安装267
3.19.2模具的使用与维护269
第4章 注塑成型工艺的设置与调整270
4.1注塑成型的原理与工艺流程270
4.1.1注塑成型的原理270
4.1.2注塑成型的工艺流程271
4.1.3塑料在注塑成型过程中的变化273
4.2注塑成型的工艺条件277
4.2.1 影响工艺条件的因素277
4.2.2注射压力279
4.2.3保压压力282
4.2.4螺杆背压284
4.2.5锁模力285
4.2.6料筒温度286
4.2.7喷嘴温度287
4.2.8模具温度287
4.2.9注射速率288
4.2.10注射量288
4.2.11螺杆的射出位置289
4.2.12注射时间289
4.2.13冷却时间289
4.2.14螺杆转速290
4.2.15防涎量(螺杆松退量)290
4.2.16残料量290
4.2.17注塑过程模腔压力的变化290
4.2.18注塑成型过程时间、温度、压力分布293
4.2.19速度-压力(v-p)的切换294
4.2.20结晶性塑料与非结晶性塑料注塑工艺对比295
4.2.21设定工艺参数的一般流程与要点296
4.3注塑成型的准备工作299
4.3.1塑料的配色299
4.3.2塑料的干燥299
4.3.3嵌件的预热300
4.3.4脱模剂的选用300
4.3.5料筒和螺杆的清洗301
4.4多级注射成型的注塑工艺301
4.4.1注射速度对熔体充模的影响301
4.4.2多级注射成型的工艺原理302
4.4.3多级注射成型的优点304
4.4.4多级注射成型的工艺设置304
4.5透明塑料的注塑工艺308
4.5.1透明塑料的品种及性能308
4.5.2透明塑料注塑前的准备工作308
4.5.3三种常用透明塑料的注塑工艺310
4.6精密注塑成型工艺310
4.6.1精密注塑的工艺特点310
4.6.2精密注塑成型的塑料材料311
4.6.3精密注塑成型的收缩问题311
4.6.4精密注塑的模具312
4.6.5精密注塑的注塑机312
4.7气体辅助注塑成型314
4.7.1工艺原理与特点314
4.7.2气辅成型的三种方式315
4.7.3关键工艺环节——气体充填316
4.7.4气辅工艺涉及的主要参数316
4.7.5气辅设备317
4.8塑件的后期处理317
4.8. 1退火处理317
4.8.2调湿处理318
第5章 注塑成型常见问题及解决方法319
5.1注塑过程常见问题及解决方法319
5.1.1 下料不顺畅319
5.1.2塑化噪声319
5.1.3螺杆打滑320
5.1.4喷嘴堵塞320
5.1.5喷嘴流涎320
5.1.6喷嘴漏胶321
5.1.7压模321
5.1.8制品粘前模321
5.1.9水口料(流道凝料)粘模322
5.1.10水口(主流道前端部)拉丝322
5.1.11开模困难323
5.1.12其他异常现象323
5.2塑件常见缺陷及解决方法324
5.2.1欠注(缺料)324
5.2.2缩水326
5.2.3鼓包328
5.2.4缩孔(真空泡)329
5.2.5溢边(飞边、披锋)330
5.2.6熔接痕330
5.2.7气泡(气穴)332
5.2.8翘曲(变形)333
5.2.9收缩痕335
5.2.10银纹(料花)336
5.2.11水波纹337
5.2.12喷射纹(蛇形纹)338
5.2.13气纹(阴影)339
5.2.14黑条(黑纹)339
5.2.15裂纹(龟裂)340
5.2.16烧焦(碳化)341
5.2.17黑点342
5.2.18顶白(顶爆)343
5.2.19拉伤(拖花)344
5.2.20色差(光泽差别)344
5.2.21混色345
5.2.22表面无光泽或光泽不均匀346
5.2.23透明度不足347
5.2.24表面浮纤347
5.2.25尺寸超差348
5.2.26起皮348
5.2.27冷料斑349
5.2.28塑件强度不足(脆性大)349
5.2.29金属嵌件不良350
5.2.30通孔变盲孔350
5.2.31内应力过大351
5.2.32白点351
5.3制品缺陷的分析与处理352
5.3.1注塑成型简介352
5.3.2制品缺陷的调查与了解352
5.3.3处理制品缺陷的DAMIC流程353
5.3.4系统性验证与分析方法353
5.3.5影响制品质量的因素354
第6章 注塑成型实践经验355
6.1提高注塑质量的关键零件与工艺355
6.1.1几种常用塑料注塑时的螺杆选用355
6.1.2注意与塑料原料相关的三个关键因素356
6.1.3注意几个影响注塑质量的工艺条件357
6.1.4注意区分注射和保压条件的设置365
6.2调机方法与技巧367
6.2.1 注塑件混色严重时的解决措施与调机技巧367
6.2.2注射量占机器额定注射量的比例越大越易产生混色367
6.2.3通过调节温度来控制生产中注塑件的颜色368
6.2.4生产中造成颜色不稳定的影响因素368
6.2.5紫色PVC件在校色和生产时的注意事项369
6.2.6一些配色颜料对注塑件强度的影响369
6.2.7提高塑件尺寸精度的注塑工艺369
6.2.8厚壁塑件缩水难题的解决技巧——表面缩凹370
6.2.9缩水问题难解决时需留意的三个工艺条件371
6.2.10硬质塑件缩水问题相对软质塑料件难解决的原因372
6.2.11大平面塑件变形问题的解决技术与技巧372
6.2.12注塑件外表面在柱位缩凹严重时的解决措施373
6.2.13 POM塑件(赛钢件)的尺寸与控制问题373
6.2.14透明的厚壁塑件注塑成型应注意的问题373
6.2.15如何通过调机来控制注塑件的装拆力374
6.2.16影响注塑件强度的几个关键工艺参数374
6.2.17镜面标识(Logo)出现熔体冲击痕的改善方法375
6.2.18浅色PVC件存放几天后出现许多麻点的原因376
6.2.19保证注塑件表面光洁的重要工艺条件376
6.2.20易造成溢边顶白而又不易引起注意的事项376
6.2.21注塑件溢边顶白严重时的多级调机方法377
6.2.22光亮塑件的表面出现许多细小麻点的原因及消除方法377
6.2.23需要快速充填时防止产生气纹的多级调机技巧378
6.2.24预防透明塑件和浅色塑件黑点多的方法378
6.2.25 POM塑件(赛钢件)生产时经常缺边少角的原因379
6.2.26浇口处容易产生气纹或射纹的条件380
6.2.27塑件的小凸台旁产生气纹的原因及调机技巧380
6.2.28 PC料注塑件产生浇口气纹难题的解决措施381
6.2.29 PC料塑件产生缩孔问题却很难解决的原因及其措施381
6.2.30延长横流道可减轻PC料注塑件的射纹和震纹382
6.2.31 PC料的注塑件变脆和起白雾的原因及其工艺问题382
6.2.32 PC件的浇口气纹成为注塑难题的原因分析383
6.2.33厚大PVC注塑件水波纹和熔接痕难解决的原因分析383
6.2.34从模具角度解决厚大注塑件水波纹难题的有效措施384
6.2.35厚大PVC注塑件水波纹和熔接痕难题的调机技巧(一)384
6.2.36厚大PVC注塑件水波纹和熔接痕难题的调机技巧(二)385
6.2.37提高塑化时螺杆的转速也可改善PVC的气纹缺陷386
6.2.38 PVC注塑件熔接痕和水波纹问题的改善措施(一)386
6.2.39 PVC注塑件熔接痕和水波纹难题的改善措施(二)386
6.2.40 PVC注塑件熔接痕和水波纹难题的改善措施(三)387
6.2.41 PVC注塑件熔接痕和水波纹难题的改善措施与技巧(四)387
6.2.42 PVC注塑件熔接痕和水波纹难题的改善措施与技巧(五)388
6.2.43 PVC注塑件表面哑色严重时的改善措施388
6.2.44注塑成型时容易产生困气问题的两个重要原因388
6.2.45关于困气的几个问题及其改善措施389
6.2.46解决熔体逆流造成的“回包”困气难题的调机方法390
6.2.47解决“死角”困气的调机方法391
6.2.48快速估算锁模力的三种方法391
6.2.49注塑模具采用小浇口的优点393
6.2.50各模腔充填严重不均衡时的调机方法394
6.2.51 K料注塑成型时顶针容易折断的应对措施395
6.2.52拆装大型模具后导柱与导套容易咬合的原因395
6.2.53电镀过的模具在注塑时制品出现拖花现象的解决方法395
6.2.54哑光面注塑件出现光斑时的现场处理办法396
6.2.55不利于注塑生产的两种滑块(行位)结构396
6.2.56调整各型腔充填速度的应用与技巧396
6.2.57将浇口和流道改大的好处397
6.2.58老旧注塑机生产POM和PVC料经常出现烧焦现象的原因397
6.2.59用小型注塑机搭配大型模具进行注塑生产的危害398
6.2.60使用长型喷嘴引发的问题及其补救措施398
6.2.61注塑生产中防止注塑件喷油、电镀不良的控制措施398
6.2.62解决低硬度软质塑件喷油后掉油的有效措施399
6.2.63注塑件生产与喷油模具的配合问题及解决方法400
6.2.64需要喷银色油漆的注塑件必须配合调机的方法400
6.2.65试模时快速设置工艺参数的方法401
6.2.66判断塑料分解程度的方法401
6.2.67调机技巧一:模具透明法401
6.2.68调机技巧二:定位注射法402
6.2.69调机技巧三:先慢后快注射法及其应用402
6.2.70调机技巧四:先快后慢注射法及其应用403
6.2.71调机技巧五压力、速度微调法403
第7章 注塑成型CAE技术404
7.1 CAE技术与M oldflow软件404
7.1.1注塑成型的CAE技术404
7.1.2 Moldflow软件404
7.2 Moldflow的操作实例408
7.2.1分析方案的选择408
7.2.2网格划分416
7.2.3网格缺陷的处理419
7.2.4分析类型与材料选择420
7.2.5浇注系统的创建424
7.2.6充填分析429
7.3实际注塑工艺在M oldflow中的设定方法433
7.3.1定义注塑机的参数433
7.3.2注塑工艺的设定437
7.3.3分析结果的优化439
7.4 Moldflow应用案例440
7.4.1制品及所用塑料440
7.4.2注塑工艺条件441
7.4.3分析结果442
第8章 注塑成型的生产管理446
8.1注塑生产的管理目标与模式446
8.1.1注塑生产管理的特点446
8.1.2注塑生产管理的目标446
8.1.3注塑生产先进的管理体系和模式447
8.1.4注塑部门的组织架构447
8.2注塑生产的流程管理448
8.2.1注塑生产的流程448
8.2.2试模管理451
8.2.3开机投产管理452
8.2.4开机投产流程图452
8.2.5不合格品处理452
8.2.6模具维修管理453
8.2.7配料和配色管理454
8.2.8上料和加料管理454
8.2.9洗机(清洗料筒)管理455
8.2.10上模(安装模具)管理455
8.2.11碎料(粉碎回收料)管理456
8.2.12落模(拆除模具)管理457
8.2.13注塑机维修管理457
8.3注塑部门各岗位职责(范例)458
8.3.1注塑部门主管(经理)岗位职责458
8.3.2注塑部门生产工程师(PE)岗位职责459
8.3.3注塑部门领班/组长岗位职责460
8.3.4注塑部门试模人员岗位职责461
8.3.5注塑部门文员岗位职责461
8.3.6注塑部门计划员/统计员岗位职责462
8.3.7注塑部门配料员岗位职责462
8.3.8注塑部门班长岗位职责463
8.3.9注塑部门碎料员岗位职责463
8.3.10注塑部门加料员岗位职责464
8.3.11注塑部门上落模人员岗位职责464
8.3.12注塑部门作业员岗位职责465
8.4注塑生产的信息化管理465
8.4.1信息化管理的重要性465
8.4.2注塑生产信息化管理的要点466
附录1常用塑料中英文名称及其收缩率468
附录2注塑成型常用术语中文、英文及俗称对照表469
参考文献471
热门推荐
- 1173141.html
- 3686921.html
- 1730838.html
- 606683.html
- 2082672.html
- 751312.html
- 2288125.html
- 88065.html
- 1219625.html
- 1339136.html
- http://www.ickdjs.cc/book_874047.html
- http://www.ickdjs.cc/book_172588.html
- http://www.ickdjs.cc/book_1698771.html
- http://www.ickdjs.cc/book_2326624.html
- http://www.ickdjs.cc/book_3812667.html
- http://www.ickdjs.cc/book_3693945.html
- http://www.ickdjs.cc/book_174269.html
- http://www.ickdjs.cc/book_2638376.html
- http://www.ickdjs.cc/book_2323827.html
- http://www.ickdjs.cc/book_878143.html