图书介绍
钢热加工数值模拟手册2025|PDF|Epub|mobi|kindle电子书版本百度云盘下载
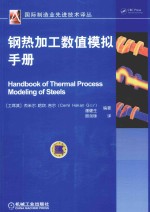
- (土)杰米尔·哈坎·吉尔(Cemil Hakan Gur),潘健生著 著
- 出版社: 北京:机械工业出版社
- ISBN:9787111531777
- 出版时间:2016
- 标注页数:505页
- 文件大小:93MB
- 文件页数:522页
- 主题词:钢-热加工-数值模拟-手册
PDF下载
下载说明
钢热加工数值模拟手册PDF格式电子书版下载
下载的文件为RAR压缩包。需要使用解压软件进行解压得到PDF格式图书。建议使用BT下载工具Free Download Manager进行下载,简称FDM(免费,没有广告,支持多平台)。本站资源全部打包为BT种子。所以需要使用专业的BT下载软件进行下载。如BitComet qBittorrent uTorrent等BT下载工具。迅雷目前由于本站不是热门资源。不推荐使用!后期资源热门了。安装了迅雷也可以迅雷进行下载!
(文件页数 要大于 标注页数,上中下等多册电子书除外)
注意:本站所有压缩包均有解压码: 点击下载压缩包解压工具
图书目录
第1章 钢热加工过程建模的数学基础1
1.1 热加工过程的偏微分方程及其求解1
1.1.1 导热和扩散偏微分方程1
1.1.2 求解偏微分方程的方法2
1.2 有限差分法3
1.2.1 有限差分法原理简介3
1.2.2 一维传热和扩散偏微分方程的有限差分求解3
1.2.3 小结7
1.3 有限单元法7
1.3.1 简介8
1.3.2 伽辽金法二维瞬态温度场有限元分析9
1.3.3 三维瞬态导热的有限元分析14
1.4 相变量的计算15
1.4.1 相变与温度的耦合作用15
1.4.2 扩散型相变15
1.4.3 马氏体相变22
1.4.4 应力状态对相变动力学的影响23
1.5 固体材料的本构方程24
1.5.1 弹性本构方程24
1.5.2 弹塑性本构方程27
1.5.3 黏塑性本构方程36
1.6 热加工中的计算流体动力学基础40
1.6.1 简介40
1.6.2 流体微分控制方程40
1.6.3 控制方程的通用形式43
1.6.4 简化后的热加工过程特定流体力学方程43
1.6.5 控制方程的求解44
参考文献46
第2章 建模方法和基本原则49
2.1 数学建模49
2.2 控制方程50
2.3 边界条件和初始条件52
2.4 控制方程的数值解53
2.5 有限单元法54
2.6 有限体积法63
2.7 蒙特卡罗法74
2.8 相场法78
2.9 结束语80
第3章 钢的热/温加工模型81
3.1 微观组织概述81
3.2 流动曲线建模——单道次81
3.2.1 热加工行为81
3.2.2 热加工本构模型84
3.2.3 动态再结晶的开始85
3.2.4 包含动态再结晶的高级本构模型86
3.3 静态再结晶88
3.3.1 Tnr方法89
3.3.2 静态再结晶建模91
3.3.3 应变诱发析出模型96
3.3.4 结合动态再结晶的先进本构模型100
3.4 晶粒长大102
3.5 相变和最终的力学性能103
3.6 温加工103
3.7 多道次条件的应力-应变和组织建模104
3.8 先进模拟和建模技术106
3.8.1 CA元胞自动机模拟107
3.8.2 MCP模拟111
3.8.3 相场模拟114
3.8.4 耦合模拟115
3.8.5 常见问题115
参考文献116
第4章 铸造模拟118
4.1 引言118
4.1.1 冶金过程的数值模拟总则118
4.1.2 铸造工艺模拟的原因及潜力120
4.1.3 解析模型和数值方法121
4.2 凝固机制124
4.2.1 均匀形核125
4.2.2 非均匀形核126
4.2.3 晶体长大126
4.2.4 枝晶长大128
4.2.5 铸锭的组织和缺陷131
4.2.6 连铸件的组织和缺陷134
4.2.7 充型与冒口136
4.3 工业铸造钢锭和钢坯144
4.3.1 连铸144
4.3.2 模铸146
4.4 铸造模拟的展望148
4.4.1 充型计算148
4.4.2 边界条件150
4.4.3 无量纲分析151
4.4.4 应力分布预测152
4.4.5 组织模拟153
参考文献155
第5章 工业热处理作业模拟158
5.1 引言158
5.1.1 热处理作业数学模型的必要性158
5.1.2 工业过程模拟和优化:挑战和方法159
5.1.3 本章结构160
5.2 工业案例研究:棒材连续退火的工艺模型160
5.2.1 连续退火作业的背景160
5.2.2 棒束退火的工艺模型161
5.2.3 工艺设计:棒束与棒的考虑162
5.2.4 基于模型调度提高生产率163
5.3 工业案例研究:冷轧钢卷箱式炉退火的集成模型164
5.3.1 箱式炉退火的背景164
5.3.2 箱式炉退火控制的传热模型165
5.3.3 传热模型的限制:集成模型的必要性167
5.3.4 箱式退火集成模型:公式和优势168
5.4 工业案例研究:渗碳作业的成本模型170
5.4.1 成本模型背景170
5.4.2 模型公式171
5.4.3 渗碳作业的最优化173
5.5 过程模型的在线运用173
5.5.1 过程模型作为软传感器173
5.5.2 以模型为基础的过程控制解174
5.5.3 基于数据的过程模型175
5.5.4 显微组织介观模型176
5.6 总结178
参考文献178
第6章 淬火模拟181
6.1 引言181
6.2 淬火过程中的相变182
6.3 淬火模拟技术现状184
6.4 传热建模187
6.4.1 简介187
6.4.2 淬火过程中的传热控制方程191
6.4.3 传热问题的有限单元公式192
6.5 相变建模196
6.5.1 简介196
6.5.2 临界温度的确定197
6.5.3 扩散型转变动力学模型199
6.5.4 等温转变模型199
6.5.5 非等温转变模型199
6.5.6 马氏体相变模型203
6.5.7 动力学参数的测定203
6.5.8 等温转变图中等温动力学参数的提取203
6.5.9 连续冷却转变图中等温动力学参数的提取204
6.5.10 应力和塑性对相变的影响204
6.6 力学相互作用建模208
6.6.1 简介208
6.6.2 本构模型209
6.6.3 混合相整体力学性能预测211
6.6.4 相变引起的塑性记忆损失212
6.6.5 力学行为控制方程212
6.6.6 淬火的热-弹-塑性公式216
6.6.7 热弹塑性问题的有限元求解220
6.6.8 相变诱导塑性(TRIP)的模拟223
6.7 FEA软件实现指南227
6.7.1 ABAQUS中的实现227
6.7.2 MSC.MARC中的实现231
6.8 总结与建议236
术语237
参考文献240
第7章 感应硬化过程模拟255
7.1 引言255
7.2 感应热处理概述257
7.2.1 感应热处理的发展257
7.2.2 涡旋电流的产生258
7.2.3 感应加热装置259
7.2.4 工件的能量吸收260
7.2.5 感应系统中的电磁效应262
7.2.6 温度分布265
7.2.7 感应线圈参数变化267
7.2.8 感应加热中的电动力268
7.2.9 淬火和冷却269
7.3 热处理线圈的建模270
7.3.1 感应线圈的要求270
7.3.2 圆柱形线圈271
7.3.3 其他“标准”热处理线圈274
7.3.4 特殊热处理线圈276
7.4 感应硬化系统模拟277
7.4.1 感应系统的物理过程277
7.4.2 电磁场278
7.4.3 材料的电磁性质280
7.4.4 感应硬化系统中的热力学过程282
7.4.5 淬火过程的换热284
7.4.6 物理建模284
7.5 数值方法285
7.5.1 概述285
7.5.2 微分模型287
7.5.3 有限差分法289
7.5.4 有限单元法290
7.5.5 积分方法294
7.5.6 数值方法比较298
7.6 关于数值优化299
7.6.1 感应加热的优化问题299
7.6.2 数值优化300
7.6.3 热处理工艺设计303
7.6.4 车轴硬化优化设计306
7.7 结论310
参考文献310
第8章 激光表面硬化模拟313
8.1 激光材料加工进展313
8.2 激光光学和光束特性319
8.2.1 单透镜聚焦319
8.2.2 焦距319
8.2.3 焦数319
8.2.4 焦点处的光束直径319
8.2.5 焦深320
8.2.6 激光束表征320
8.3 激光吸收率321
8.3.1 温度的影响321
8.3.2 吸收测量技术326
8.4 激光表面硬化335
8.4.1 激光加热和冷却335
8.4.2 激光硬化过程中的冶金学337
8.4.3 钢的奥氏体化342
8.4.4 硬化深度的数学预测355
8.4.5 计算温度循环的方法362
8.4.6 热流模型365
8.4.7 材料激光硬化和熔化的热分析371
8.5 激光表面硬化后的残余应力376
8.5.1 背景376
8.5.2 热应力和相变应力的测定377
8.5.3 计算残余应力的简单数学模型382
8.5.4 用数值模拟方法确定应力386
8.5.5 评估残余应力分布的简单方法393
8.5.6 预测硬化轨迹和优化工艺397
8.5.7 模型应用400
8.5.8 经激光表面重熔处理的微观组织分析405
参考文献413
第9章 表面硬化数值模拟419
9.1 引言419
9.2 渗碳表面硬化技术420
9.3 渗氮和碳氮共渗表面硬化技术422
9.4 表面硬化模拟的多场耦合426
9.4.1 模块1)碳和氮同时扩散和析出427
9.4.2 模块2)传热433
9.4.3 模块3)相变434
9.4.4 模块4)应力应变分布437
9.5 残余应力和工件性能的关系438
9.6 文献典型实例439
9.6.1 不同角度楔形板的渗碳工艺439
9.6.2 纯铁脉冲离子渗氮过程中氮化层的生长及氮在ε-Fe2-3N、γ′-Fe4N和α-Fe中的分布443
9.6.3 铁素体马氏体双相不锈钢高温气体渗氮过程中马氏体层的生长动力学444
9.6.4 渗碳钢中多相相变的有限元研究449
参考文献454
第10章 热处理和化学热处理计算机模拟的工业应用460
10.1 阶梯轴的加热CAE460
10.1.1 三维温度场计算机模拟的实验验证460
10.1.2 优化加热工艺的CAD技术461
10.2 复杂形状零件淬火工艺CAE/CAPP463
10.3 曲轴渗氮畸变控制CAE465
10.4 气体渗碳CAE/CAPP/CAM466
10.4.1 齿轮渗碳工艺CAE466
10.4.2 智能型密封箱式炉生产线CAM468
10.5 基于计算机模拟的动态可控渗氮技术473
10.6 热处理设备的智能CAD474
10.7 大型钢模块淬火冷却虚拟生产476
10.7.1 P20塑料模具钢淬火工艺模拟与设计476
10.7.2 静止水淬火480
10.7.3 小结481
参考文献483
第11章 钢热加工过程建模的展望485
11.1 热加工过程建模与计算机模拟存在的问题485
11.1.1 工程技术方面的问题485
11.1.2 基础理论方面的问题486
11.2 热加工过程建模与计算机模拟的发展趋势493
11.2.1 材料加工成形的建模与模拟的发展趋势493
11.2.2 热处理与表面改性的建模与模拟的发展趋势499
11.2.3 高集成度的产品CAE技术502
参考文献503
热门推荐
- 667519.html
- 1403348.html
- 2821908.html
- 3800816.html
- 2305317.html
- 1244165.html
- 723107.html
- 3649573.html
- 3336316.html
- 2648179.html
- http://www.ickdjs.cc/book_2290576.html
- http://www.ickdjs.cc/book_3250762.html
- http://www.ickdjs.cc/book_2772997.html
- http://www.ickdjs.cc/book_1435050.html
- http://www.ickdjs.cc/book_372632.html
- http://www.ickdjs.cc/book_99614.html
- http://www.ickdjs.cc/book_3168905.html
- http://www.ickdjs.cc/book_1291008.html
- http://www.ickdjs.cc/book_1584262.html
- http://www.ickdjs.cc/book_138386.html